
All raw materials and fittings are bought from Mcmaster-Carr. Total cost comes out to $137.53. Itemized budget is shown in appendix D. Mainly round stock is required for the majority of the parts to be machined out of. All parts that show in the parts list in appendix C that are not shown in the budget are already owned. Labor is valued at $100 per hour with no outsourced labor. Tentative schedule as shown in appendix E predicts 150.4 hours of labor is required, making the total labor cost equal $15,040. Although labor is valued at $100 per hour, it will be completed by a willing engineer accepting $0 per hour, putting total project cost at $137.53. Funding may be sourced from CWU, however if CWU does not accept request, it will have to be funded by the engineer (regardless of his/her) poor financial status.
After all the raw materials and pipe fittings were bought, the total cost came out to $140.27. This is close to what was budgeted as no deviations in the parts list has been made so far. All parts were ordered from McMaster-Carr as predicted and they all were delivered in a timely manner. All raw steel material ordered from McMaster-Carr was delivered within the tolerance specifications promised by the website. However, there are future plans to manufacture more nozzles out of ceramic so they can be used long-term instead of oxidizing away like the steel one. Machinable ceramic will be ordered from Maryland Lava Company. Pricing is not shown on the website, and scrap material will be requested to avoid going too far over budget.
Most of the unexpected expenditures came from the testing setup. It was assumed that the testing wouldn't cost anything since the forge was already owned. However, the forge required repairs before the testing could be done, so more insulation bricks were purchased. This added $62.87 to the final cost. A thermocouple also needed to be purchased to measure the forge temperature. The thermocouple cost $46.06, bringing the total testing cost to $108.93. After adding the cost of testing materials, the total material cost for the project was $249.20, this was 181.2% the predicted material cast for the project.
Schedule
The main deliverables for the project are the proposal with an initial design for the burner, parts that need machining, full assembly of device assembled with purchased parts, and a full test of the device with a testing report. The proposal for the project with the design is to be completed before December 6th, and all changes to design must be completed before the following January 7th. A fully assembled device must be completed before March 13th with various milestones for machined part completion in between. Testing will begin on March 31st and a full report of the test will be completed before June 5th. All individual tasks are scheduled in appendix E with predicted time constraints for each task.
The manufacturing process deviated from the original plan because the order of parts being manufactured needed to be changed. The original plan was designed so the most difficult part (the Intake) was made first. That way the hardest part was done first, and a lot of other parts attach to it, so they can be fit up as they are manufactured. The manufacturing order ended up being dictated by when raw material can be obtained. The injector was made first because the stock could be bought at ACE, and the injector bracket was made next because it was made from scrap. The rest of the parts are made from raw material from McMaster-Carr.
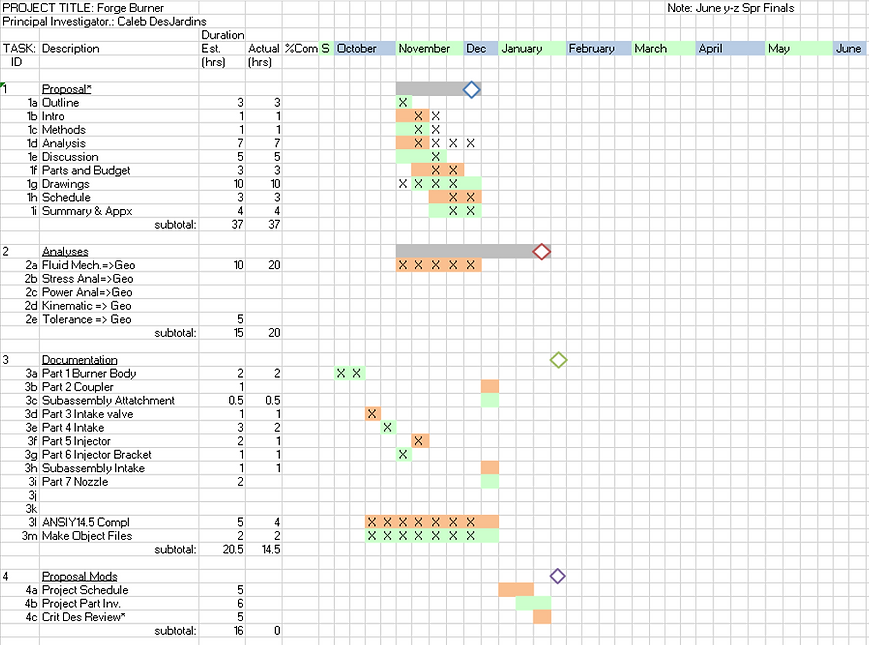
