Testing
The variables being tested for the forge burner are the time to bring a forge to temperature, amount of fuel used, and the oxidation of parts put in the forge. These variables are an indication of the performance of the burner because an improper air/fuel mixture will either cause over-oxidation, inadequate heating, or a waste of fuel.The forge will start cold in the testing and both burners will be timed to reach 1000 °F with the thermocouple placed under the floor brick. The tests will have to take place on different days to make sure the forge is fully cooled between tests. The propane tank will be weighed before and after the test to gage fuel consumption. Oxidation testing will be done by maintaining 15 psi of propane pressure and placing a piece of steel in for a given amount of time. Plain carbon steel will be used for the test as it has a higher affinity for oxidation. The tests will be completed with the engineered burner and with a black iron pipe benchmark burner, and the two will be compared.
Results
Discussion
The final design of the burner is successful as it has the required geometry to achieve the requirements. However, most of the analyses may not be a success as different approaches were analyzed for solving the flow rates and are more accurate than the previous approach. Changes in flow rate analyses did not affect the overall design, however it will affect the graduations that will be stamped into the side of the injector bracket and it affected the inner diameter of the burner body. The final assembly after the manufacturing process was successful in incorporating all of the critical geometry. The testing indicated improvements to the benchmark in every aspect; which varied from the prediction as the forge burner was assumed to improve in only two of the three aspects. The forge burner was promising from the beginning based on the sound. The benchmark had a choppy burn at first and took a while to even out, whereas the engineered forge burner gave a smooth flame throughout the test. The time to heat test showed a 16.2% improvement which fell short of the projected 20%, but it was a significant improvement nonetheless. The propane consumption was a huge improvement as the engineered forge burner consumed 53.6% as much fuel per minute than the benchmark burner. The oxidation sample for the benchmark showed much more surface distortion than that of the engineered forge burner; samples are shown in Appendix G5.
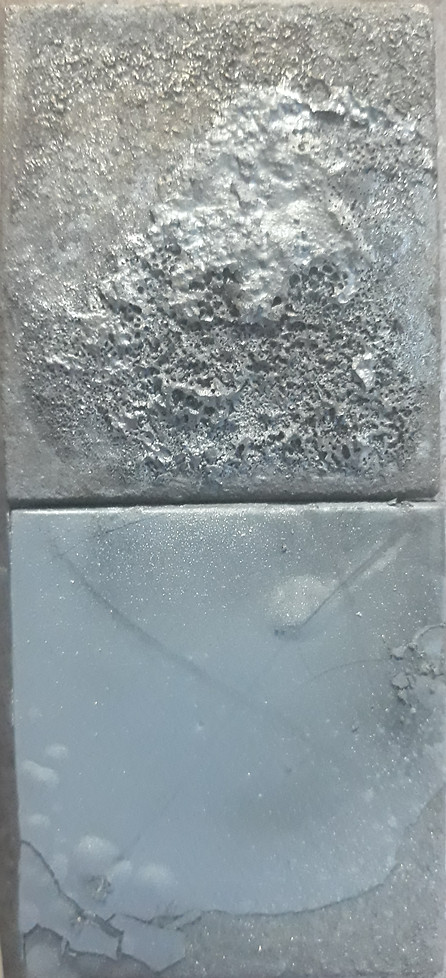